Rinsing for Recovery, Efficiency, and Better Work
This reviews practical and proven rinsing techniques which ensure high quality standards, minimize the amount of water necessary and provide for recovery of most, if not all,of the process dragout.
The formulas required for exact calculation of rinse ratios and water requirements are cumbersome; they have been avoided in this presentation. Those calculations included in the following images are simple estimating formulas adequate for everyday use.
We will demonstrate superior rinsing techniques with considerably less water flow than that provided by Niagara Falls.
In The Beginning
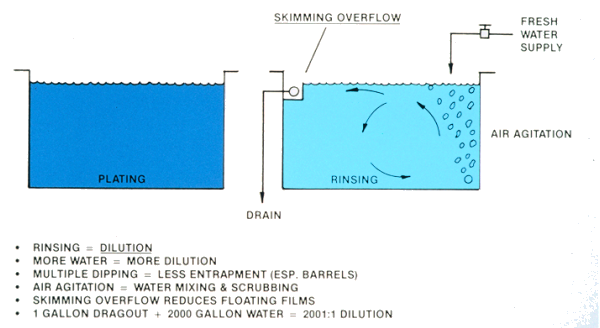
- Most of us see the rinsing operation as removing a process solution from the
surface of the work.
- In practice, rinsing is the act of diluting the process film on a work surface, to
the point that the low concentration of this film is no longer objectionable.
- In this discussion, we will look at the most common from of rinsing—immersing
the contaminated work in a tank of running water—as pictured here.
- Looking at the captions:
- Rinsing is done by Dilution.
- A higher flow rate from the “fresh water supply” produces more dilution.
- Multiple dipping of the work into the rinse tank produces a Flushing action to
reduce entrapment– especially important in barrel plating.
- Air agitation across the bottom of the rinse tank– away from the “overflow”
produces a rolling motion and pushes any floating films toward the
“skimming overflow”.
- Over any period of time, say one hour, when 1gph of dragout is mixed with
2,000 gallons of clean water, the dilution ratio is 2,001 to 1.
Someone Decided To Save Water
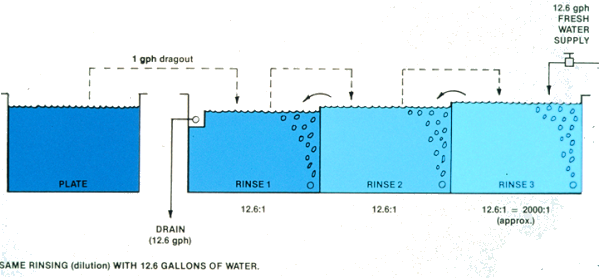
- This image shows a process tank followed by 3 counterflowed rinses. 12.6 gallons
per hour of clean water is introduced into the last rinse tank and counterflowed by
gravity through rinse 2, then rinse 1, and finally to drain. Each piece of work sees the
same water stream 3 times--in progressive cleaner tanks.
- The dilution of the film on the work is about 12.6 to 1 in each rinse station,and we can
say that the “work film” is 12.6 times more dilution each station. This gives us a total
dilution of about 2000 to 1.
More Sophistcation: The "Save Rinse"
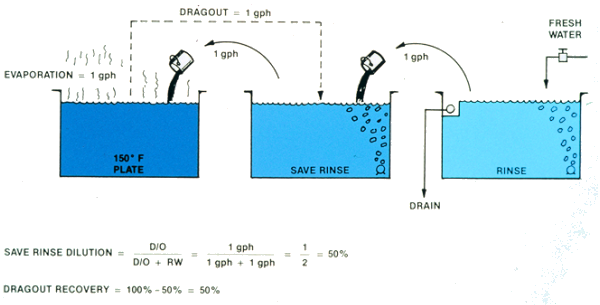
- If the volume of drag-in and dragout are equal at the process tank, then the solution
level will be reduced only by surface evaporation.
- This image shows an evaporation rate of 1 gph, due to the 150° F solution temperature.
This fact allows us to “bucket” 1 gph from the “save rinse” to the process tank.
- Reasoning alone tells us: if the dragout of 1gph is mixed with 1gph water, then the
mixture in the “save rinse” is 50% concentration of the process tank.
- The formula for dilution in one rinse is—dragout, divided by rinse water plus dragout.
- Since we are returning 1 gph of 50% diluted solution—the recovery rate is 50%.
- Here, final rinsing is done in an overflow rinse tank.
Getting It Together!
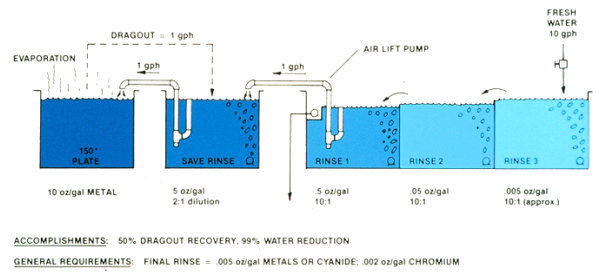
- In this image we see a combination of the water-saving counterflowing arrangement
and the “save rinse.”
- As we established in the last image the dilution or rinsing in the “save rinse” is 50%
in this case. Evaporation from the process tank remains at 1 gph.
We are using simple “air lift pumps” to transfer solution.
- The first printed line under the tanks indicates the reduction of metal (in ounces per
gallon) at each rinse station.
- The next line shows dilution ratios
2:1 x 10:1 x 10:1 x 10:1 = 2000:1 (approximately).
- We are recovering 50% of the dragout and saving 99.5% of the water required for a
single rinse.
- The generally acceptable contamination of the final rinse is .005 ounces per gallon
of metals or cyanide, or if rinsing chrome, .002 ounces per gallon.
Best Of All Worlds
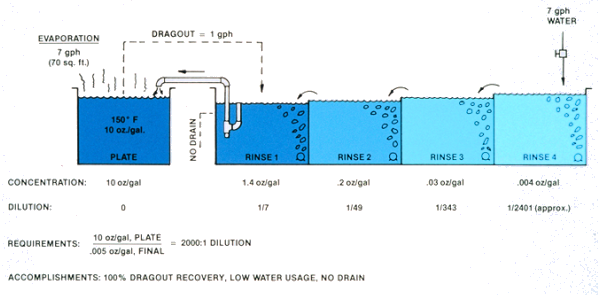
- This image has a few changes
- The process tank evaporation has been increased to 7gph—the “rule of thumb”
is 1/10 gph evaporation per square foot of solution surface area at 150o F.
- We have 7 gph flowing through the 4 rinses to balance the 7 gph evaporation.
- We have eliminated the drain.
- The first printed line shows solution concentrations, ending up with .004 ounces per
gallon in rinse 4.
- Total dilution is about 2401 to 1.
- The dilution requirements are defined as 10 ounces per gallon process solution
divided by .005 ounces per gallon final rinse—or 2000 to 1.
- We have 100% dragout recovery, low water usage (7gph) and no drain.
To Increase Process Tank Evaporation...

- A simple and inexpensive method to increase evaporation from a process tank is to
use an “Atmospheric Evaporator.”
- In this case, process solution is circulated and sprayed inside the evaporator—
Blower air is forced past the sprayed solution—picking up humidity.
This humid air passes through an efficient “mist eliminator” to remove any
airborne solution droplets. The humid air should be ducted to the outdoors.
- In this diagram, as the process solution level drops, due to evaporation, a level control
turns on a solenoid valve, allowing more rinse water to flow.
- The results: 100% recovery, no waste treatment, no drain.
How Much Rinse Water Do You Need?
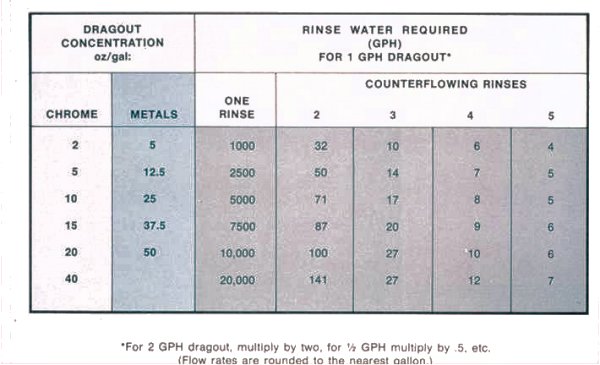
- This table is based on the final rinse having .005 oz./gal. metals or cyanide, or .002
oz./gal. Chromium. Flow rates are based on 1gph dragout—you can double the
flow rates for 2gph dragout, etc.
- On any line, you can see how dramatically the required flow rates drop when we
add counterflowing rinse stations.
Evaporation

- With an atmospheric evaporator, the rate of evaporation is determined by:
- Size of evaporator
- Temperature of the solution and air
- The relative humidity
NOTE: The evaporation rate of room temperature solutions is affected directly
by relative humidity. Relative humidity has less effect on higher temperature
solutions.
Cold Process, High Evaporation Rate

- This diagram shows the addition of a new, heated tank.
- A cold process tank may not provide the heat required for enough evaporation to
satisfy the rinsing requirements.
- Rinse water containing dragout is collected in the new, off-line heated tank.
The evaporator reduces the water in this tank. Dragout concentrate can be
returned to the process tank as needed.
Cold Process, Limited Space

- Almost any rinsing situation can benefit by using an evaporator. Difficult situations
include those that have:
- Few rinse stations
- High dragout rates
- High dragout concentrations
- Low process tempurature
- This image shows dragout being recovered from the first two rinses only. The last rinse
is supplied with enough running water to ensure clean parts.
- A small rate of evaporation will recover a high percent of the dragout.
Full Or Partial Recovery?
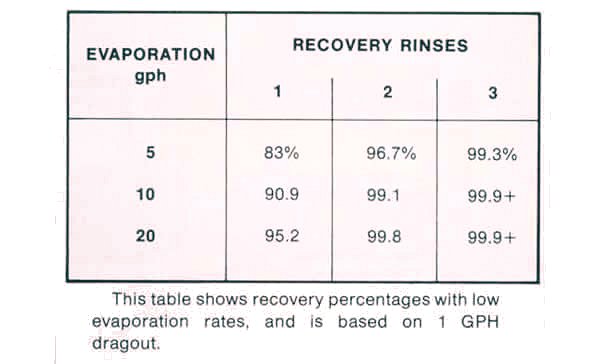
- This table shows the high percentages of dragout recovery that are obtained with
very low evaporation rates. The table is based on 1 gph of dragout.
- Note that when using only 2 recovery rinses and 10 gph of evaporation, dragout
recovery is over 99%!
- But, in most cases, a final running rinse is required for complete rinsing.
Uses for Atomspheric Evaporation
- Reclaims Dragout - About 95% of plating chemicals used due to dragout.
- Reduces "Waste Treatment" - Lower chemical usage, less sludge, less hauling.
- Helps Control Temeratures on Cold Solutions - Also takes heat from heated solutions.
Heat for Evaporation = 8090 BTU/Gallon
- Makes Room for Liquid Adds to Cold SOlutions - Controls "growing" solutions.
- Reduces the Volume of Waste Solutions.
The Poly Products Evaporator
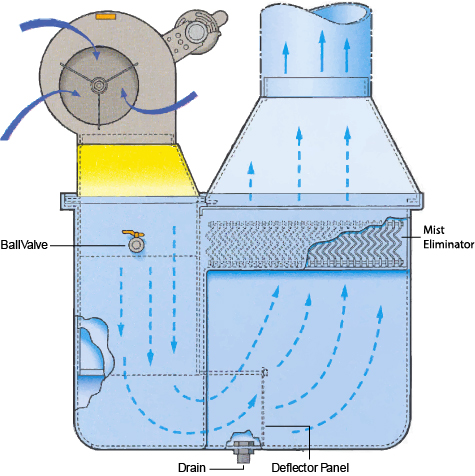